Developing Continuous Improvement: Definition, Key Steps and Tools
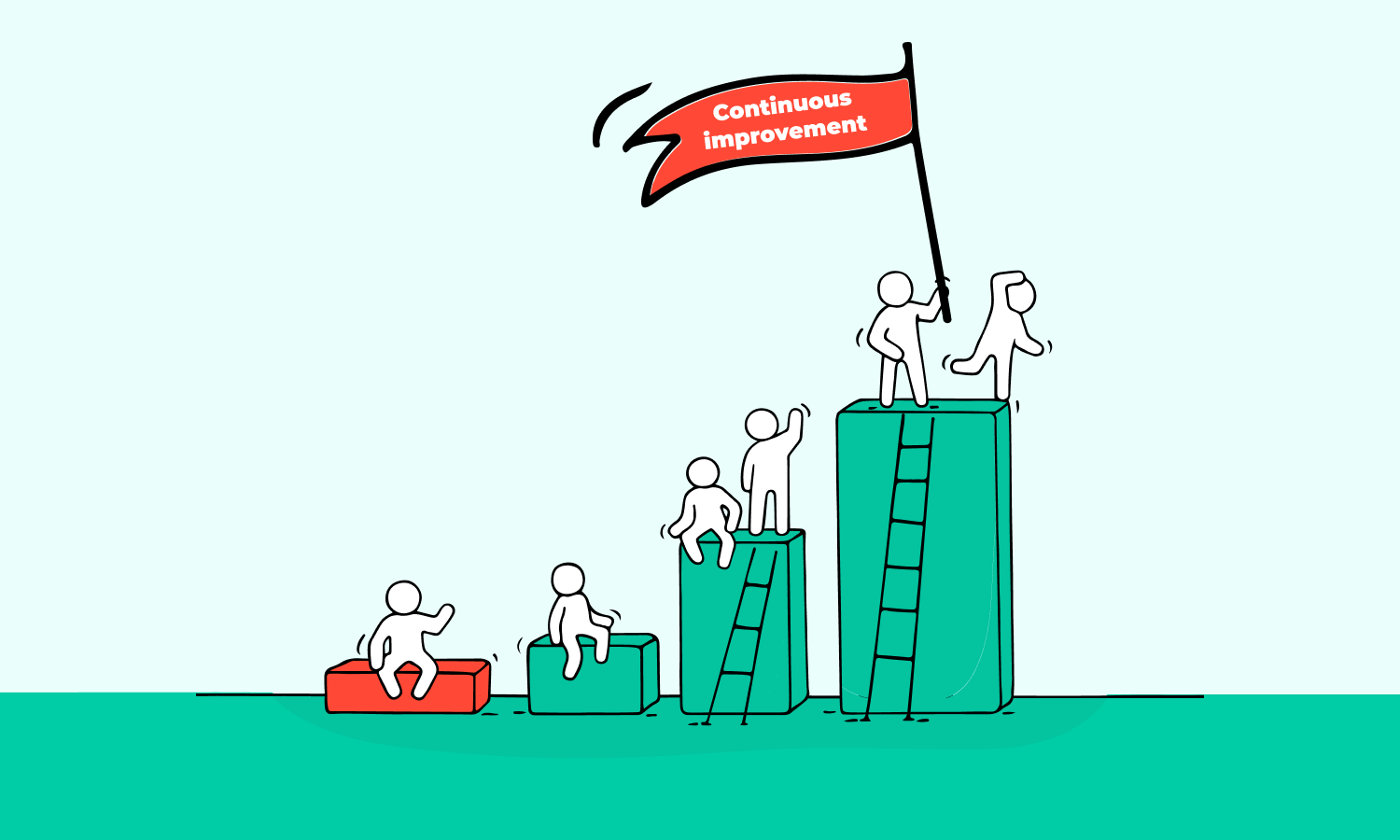
There is no perfect process. However, there is always room to improve something. Many teams have no chance to identify, test, and implement the changes they make. Each tweak in their case is like a blind game.
To get better results, you need a continuous improvement program. It will ensure that the changes you make will not make your operations a lot harder.
Successful changes can make employee’s jobs easier and more pleasant to perform. They will help you to save time and money. You will also get far better value out of your current efforts and operations.
In Lean management, continuous improvement is like a religion. In order to implement this concept, you need to have a clear understanding of what it means, what tools you need to apply and check some of the best practices.
So, what is continuous improvement and why is it important? What are the steps in continuous process improvement you need to follow? Let’s find the answers in our article.
What Is Continuous Improvement?
Continuous improvement (also known as Kaizen and continual improvement) is a practice of identifying opportunities for streamlining work and reducing waste.
This method was conditioned by the popularity of Lean and Agile approaches in manufacturing and business areas. Nowadays thousands of companies all over the world use continuous improvement to identify savings opportunities. Many of these ideologies provide outstanding results. You may successfully apply both Kaizen and Kanban to facilitate continuous improvement.
When should continuous improvement be used?
In order to maintain quality standards while cutting costs and time, businesses turn to Lean ways of working, including continuous improvement. Keeping in mind best continuous improvement practices, companies are able to find ways to continue business as usual while analyzing improvement opportunities along the way.
The teams that cannot practice a continual improvement plan throughout their day-to-day work can follow the way to leverage the concept is to hold continuous improvement events (also known as Value Stream Mapping).
Depending on the depth of the covered topic, continuous improvement events can take 1-5 days to complete.
Many businesses have adopted Lean techniques as a standard. Continual improvement helps them to save money by identifying inefficiencies in project teams.
The decision about making continuous improvement part of a company’s everyday culture or not depends on organizational attachment to the cost savings that may occur as a result.
Breakthrough and Incremental Improvements
Kaizen is typically practiced by applying two disciplines: incremental and breakthrough continual improvements. A good idea to deploy a Kaizen program is to combine them both.
- Breakthrough improvement represents large changes to a method/process, usually by reviewing the item with your team and deciding on what to do altogether. This approach requires more costs (in money and time) than an incremental improvement. However, it results in bigger revisions. By running a breakthrough meeting you will let everyone stay up to date while making sure that the process is as good as it can be.
- Incremental improvement means small changes to a method/process with the aim to optimize it as problems are identified. It typically costs less and can be implemented faster than using a breakthrough way. Let’s say, incremental improvement is about making small corrections without having to review the entire operation.
What Are the Benefits Continuous Improvement Provides?
There are two main advantages of continual improvement:
1. Streamlining workflows
When you work to constantly improve, you and your company can reduce operating overhead. The continuous improvement process represents a Lean improvement technique that helps to optimize workflows. Lean ensures effective workflows that save money and time and allow reducing wasted time and efforts.
2. Reducing project costs and preventing overages
Project managers must know the costs of completing a body of work. Therefore, PMOs (project management offices) benefit from knowing the amount of time it takes to get particular types of work done. As a PM, you can reduce project costs and prevent overages using special forecasting software.
How to Create a Continuous Improvement Process?
There are special activities that may be performed by a process improvement team (sometimes referred to as an SEPG – software engineering process group). Here are these process factors you need to consider for continuous improvement:
1. Identify improvements
Identifying potential improvements within your company may not be so obvious. One of the more efficient strategies your process improvement group can apply is to help teams adopt the practice of holding regular retrospectives. Retrospectives are common for disciplined Agile delivery teams. However, sometimes it is a new concept for data management teams, architecture teams, IT governance teams, and so on.
You may choose any way to share improvement ideas between teams. Many of these ways are free or at least very inexpensive to implement. It can be an internal discussion forum, practitioner presentation, or a Lean coffee session where people voluntarily meet at a regular time to share ideas.
3. Capture improvements
Identified improvements should be captured to retain them over time. Your team may describe each learning in a document and then manage it in a documentation repository or capture the learnings in a shared wiki such as Confluence. Another way to describe the evolving process is to use an expert system (such as Enterprise Transformation Advisor).
4. Support teams
Education and training are the ways your process improvement team can utilize to help others to adopt process improvement techniques. They may also facilitate retrospectives and team assessments. Coaching and training will help to see that they can safely try new ideas within their environment for a few iterations to understand whether it works for them or not.
5. Initiate communities of practice
CoP (a community of practice) is a group of people who share a profession and who collaborate to learn from each other to develop themselves and their business. There are CoPs for architecture, testing, Agile, business analysis, technical debt, etc. A CoP often starts when one or several team members recognize the need for it. Usually, participation in the CoP is voluntary.
6. Initiate centers of excellence
CoE (a center of excellence) is a gathering of people with specialized skills and expertise with the purpose to provide leadership and disseminate that knowledge within the company. The CoE is often created to support the adoption of new technologies. Its creation is often a key component of the organization’s overall Agile transformation efforts.
7. Govern improvement
Senior management usually wants to know whether or not the company is benefiting from your investment in adopting Agile and Lean approaches, as well as how much things are improving, and how widespread the adoption is. It is better to have some way to monitor and report on in a lightweight manner.
How to Adopt Continuous Improvement? Popular Tools and Techniques
In order to set yourself up for continuous improvement, you need to build a proper environment within your company. Lean management contains three major approaches for achieving continuous improvement:
RCA
RCA is Root Cause Analysis – a technique that allows achieving a continual improvement plan by showing you the root causes of your process’s problems.
This iterative practice drills down into a problem by analyzing what caused it until you reach the root of the negative effect. In order to apply the method, you will need to perform a thorough analysis of the problem. It is better to analyze each problem’s root cause and experiment with solutions.
Problems may often turn out to be more complex than you think. In this case, RCA will require a few iterations before preventing the negative effect from ever happening again.
PDCA
PDCA means Plan-Do-Check-Act. This model is the most reliable approach for achieving continuous improvement. The main goal of this never-ending cycle is to help you improve further based on achieved results. Initially, PDCA was developed for quality control but then it became a tool for achieving continuous improvement.
At the first step – the planning step – you will need to establish the objectives and processes necessary to reach results in accordance with the expected output. Setting output expectations is key to achieving continuous improvement as the accuracy and completeness of the goals are a major part of the process of improving.
The next stage is “Do” where you will need to execute what you’ve laid down during the process’s planning step. Then you will need to check what you’ve achieved and compare it to what you’ve expected. Consider what you can improve in your process to get better results next time.
Lean Kanban
If you want to continuously improve your process, you need to clearly visualize what needs to be improved. Toyota was the company that developed Kanban as a system for improving the workflow efficiency of the production process when it was looking for a way for visualization.
Then Kanban was adapted for knowledge work and now it helps thousands of teams to achieve continuous improvement models. This approach relies on 6 practices for minimizing the wastes in your process:
- Visualize your workflow
- Eliminate interruptions
- Manage flow
- Make process policies explicit
- Create feedback loops
- Improve collaboratively
The method offers reliable Kanban boards for mapping every step of your process. These boards are divided by vertical lines forming columns for the different stages. Here’s how it looks in Hygger:
A basic Kanban board has three columns: To Do, In Progress, Done. Each task you or your team is working on is placed on a Kanban card. It needs to pass through all the stages of your workflow to be considered complete.
Kanban boards show you the amount of work that every team member has and can help you prevent overburden by allowing you to delegate tasks. The main goal is to eliminate multitasking that only harms productivity.
Bottom line
Kaizen is a group activity. Therefore it is important to ensure that your team completely understands the common goal and why their part of the process is important.
Continual improvement is a never-ending quest for perfection. However, when your team takes it by heart, you will definitely start feeling the benefits of Kaizen on your business. The tools mentioned above can help you with that as your team will obtain lots of knowledge about process and workflow improvements.
Consequently, everyone will understand how your process works and how it can be improved.