What Are the Most Popular Six Sigma Tools?
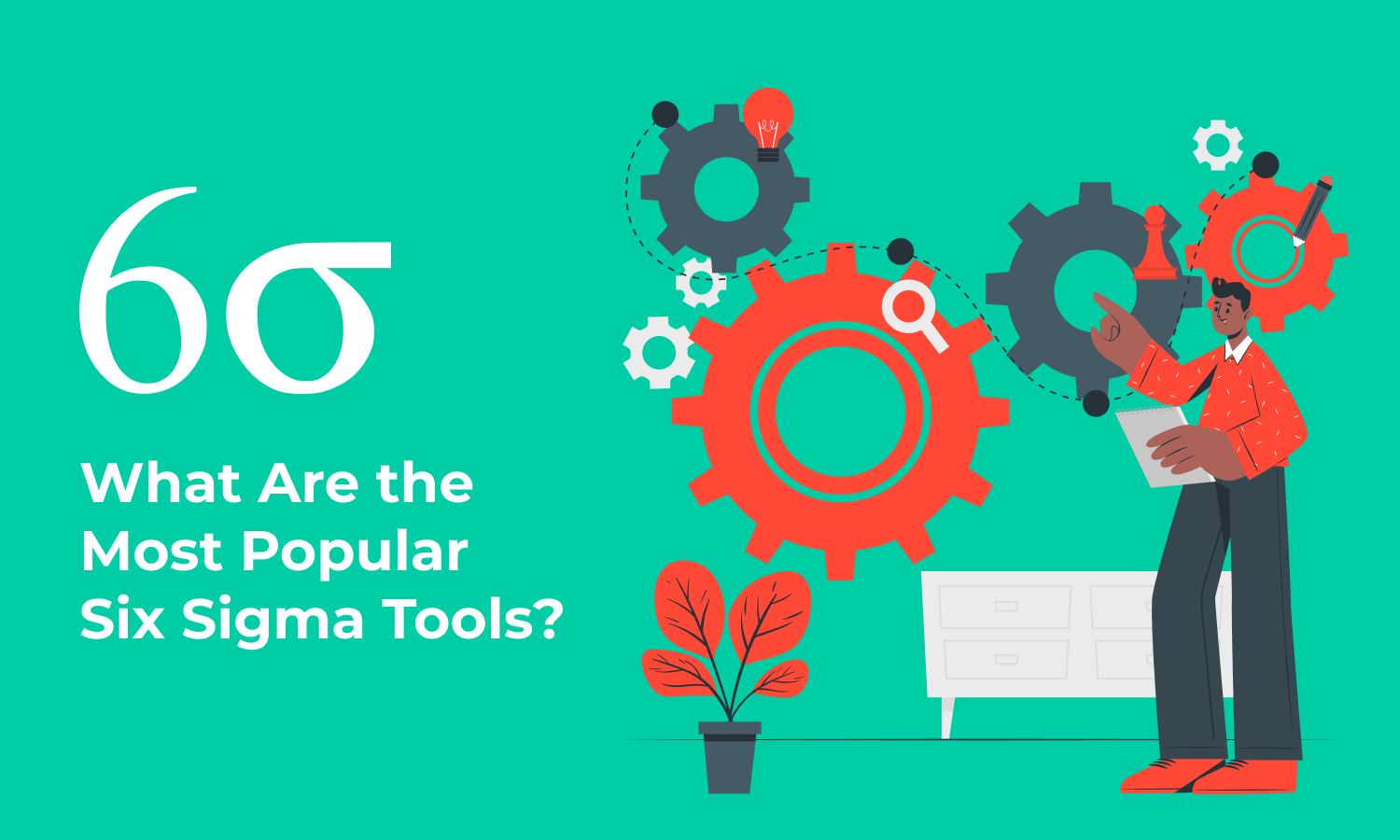
If you still seek a method of eliminating processes defects and waste, then Six Sigma is what you need. This powerful management methodology also helps to reduce variations in business processes to the barest minimum.
Nowadays many companies all over the world apply different Six Sigma tools to drive systematic and strategic improvements in their business processes.
Professionals who learn the method and get various Six Sigma belts as professional certification make use of these tools to implement improvements. Have you heard about such tools are Value stream mapping, 5 Whys, or Pareto Chart? These tools and many other approaches represent the family of robust and helpful Six Sigma tools and methods.
Executing Six Sigma projects, your project team will definitely use a systematic model called DMAIC, which simply means define, measure, analyze, improve, and control. DMAIC focuses on these five major areas used in implementing Six Sigma projects. Each of the areas involves the use of a different set of tools.
Six Sigma tools are important for management as the ultimate goal of every business is customer satisfaction. And constant quality improvement is key to achieving this satisfaction.
So what are these powerful tools used for Six Sigma projects? Let’s dive into details of some of the most popular of them.
What are the Tools of Six Sigma?
1. Project Charter
This is a document that defines the scope of the project and its purposes. It works as the blueprint for the business process and as the project legal authorization.
The project charter contains the project overview and its scope with all details about the team, resources, and timelines. It provides the basic info about the project and clarifies its core aspects. The main benefit of this doc is that it reduces chaos.
Working on the project, the team can easily lose track of who is responsible for what, which deadlines the team has to meet, and so on. The project charter helps you to keep a focus on what your project is all about. It literally assists you in bringing your business back to order when things get confusing.
2. 5 Whys
Companies often notice that one and the same problem may occur over and over again. It keeps creeping back in at a later date, no matter how many times they address it. In order to get to the root of such chronic problems, you may use the 5 Whys tool that originated in the 1930s with the Japanese industrial revolution.
The 5 Whys is rather simple: when the problem arises again, you should understand the cause by asking “why” five times. This approach looks most effective when used to deal with moderately difficult challenges. If there are more complex problems, you may achieve better results by using a cause-and-effect diagram.
Do not underestimate this method, as its simplicity is what makes it powerful and helpful. It works well in combination with other Six Sigma tools.
3. 5S System
The 5S system refers to the methodology of organizing workplace materials for quicker access and better maintenance. It is essential for liquidation waste that is produced by poor workstations and tools in poor condition.
The 5 S elements are:
- Sort – remove unnecessary items for your current production. Leave only what is really necessary.
- Set in order – organize remaining items and label them.
- Shine – clean and inspect your work area and everything in it.
- Standardize – write out your standards for all the steps.
- Sustain – apply the standards you’ve set for your company and make them habits for everyone in your team.
4. Kanban
Kanban system is a management chain control system focused on cost reduction by implementing a just-in-time inventory control approach. This high-demanded Six Sigma tool provides ease of use and obvious benefits.
Kanban literally means billboard form Japanese. This term was coined by an industrial engineer at Toyota, who based his system on how supermarkets control their inventory.
Popular Kanban boards set limits for the inventory-holding for all current business processes. It allows you to free additional resources, using them better. In fact, Kanban is based on a simple and elegant idea: only activate the supply chain when the demand requires it. It brings more focus to the business process itself and increases its efficiency.
5. Pareto Chart
Pareto Chart represents the famous Pareto principle, claiming that 20% of input produces 80% of output in any given situation.
The Pareto chart contains a vertical bar graph and a line graph. The vertical graph shows the metrics of different business process components from the largest to the smallest one. The line graph is the cumulative total of these metrics.
This tool demonstrates what part of the process affects the result the most. In order to build this chart, you need to figure out the components of the process and understand how to measure them. Then you can put this data into the chart. You will see how big of an influence on the outcome each component has.
6. Business process mapping
Process mapping as a method represents a visual way to reflect the business process and better understand how it works. A map outlines the standards, roles, and responsibilities. This data is presented in a structured way. They demonstrate the steps of the process with all responsible sides, what the inputs and outputs are, and other relevant info.
Process mapping is a robust problem-solving tool that visualizes the entire process, making it easier to understand what’s wrong and what ate the root cause. Moreover, business process mapping seems great for finding the potential risks the process creates.
7. Responsibility assignment matrix
Responsibility Assignment (RACI) matrix is a table that describes the responsibilities of each team member regarding all the tasks of the business process.
The table includes four components:
- Responsible – their role is to achieve the task.
- Accountable – people who assign tasks to others and monitor their progress.
- Consulted – the experts on the subject matter whose opinions guide those working on the task.
- Informed – the individuals you notify once you complete the task.
These are the key responsibilities most commonly used in the matrix. The RACI matrix allows you to see the gaps in the team structure and which roles you have to fill.
8. Regression analysis
This statistical process is used for understanding and estimating the relationship between variables.
It helps to define the mathematical relationships between an output variable (y) and any number of input variables (x1, x2, etc.) With the graphical view of these inputs and outputs, you can visualize patterns or deviance from desired patterns in your workflow.
9. Fishbone diagram
The Fishbone diagram actually resembles a skeleton of a fish. This diagram is also known as a cause-and-effect analysis diagram. This handy and famous Six Sigma tool allows you to brainstorm various causes of different problems.
First, you have to identify the problem you want to solve. Write down who works on the process as well as when and where the process occurs. Then, write the problem in a box on the left-hand side of the paper. Draw a horizontal line extending to the other end of the paper. After that, draw vertical lines extending off of the “spine”. Note the key reasons behind the problem. Think through any possible causes. These causes can be broken down into sub-causes.
Completing the diagram with possible problems’ causes will help you to analyze your results.
10. Kaizen
Kaizen (Continuous Improvement) refers to the practice of continually observing and implementing incremental improvements in the manufacturing process. The tool involves managers and employees in the process of manufacturing improvements.
Applying Kaizen means that waste will be gradually reduced through the collective talents and knowledge to change the smallest inefficiencies every day.
11. Value-stream map
This kind of map describes the information and materials required to bring the product to clients. It is used for streamlining the production process.
You may most likely see the appliance of value-stream mapping in Lean manufacturing, but it can be also useful for businesses in almost any industry.
Value-stream mapping strives to visualize such information as time, error rate, and unnecessary delays within the process. The map includes the following parts:
- the process map that includes each of the steps involved in the business process.
- the timeline that comes from the process map and summarizes all the data on the duration of the process.
- the information flow that explains how each of these steps interacts with each other.
12. Voice of the customer
Another Six Sigma tool used to implement improvements is The Voice of the Customer. Organizations use this tool as a proactive measure to gather feedback from customers about their expectations, needs, and experiences.
They can tailor their processes or products to meet and exceed all expectations of clients. Businesses can define the Voice of the Customer by engaging them in interviews and conversations.
Takeaways
Businesses apply Six Sigma tools to eradicate defects and waste in their processes. These tools are reliable methods and techniques employed in implementing Six Sigma projects. They help companies to increase efficiency and profitability and reduce costs.
Tools for Six Sigma can suit any type of business process. However, Six Sigma projects must pass through all the stages of DMAIC.
If you strive to deploy Six Sigma tools in your company’s processes, you’ll definitely achieve quality improvements. After all, continuous process improvements will help you attain customer satisfaction and loyalty.