What is the Key Value of Quality Function Deployment in Product Development?
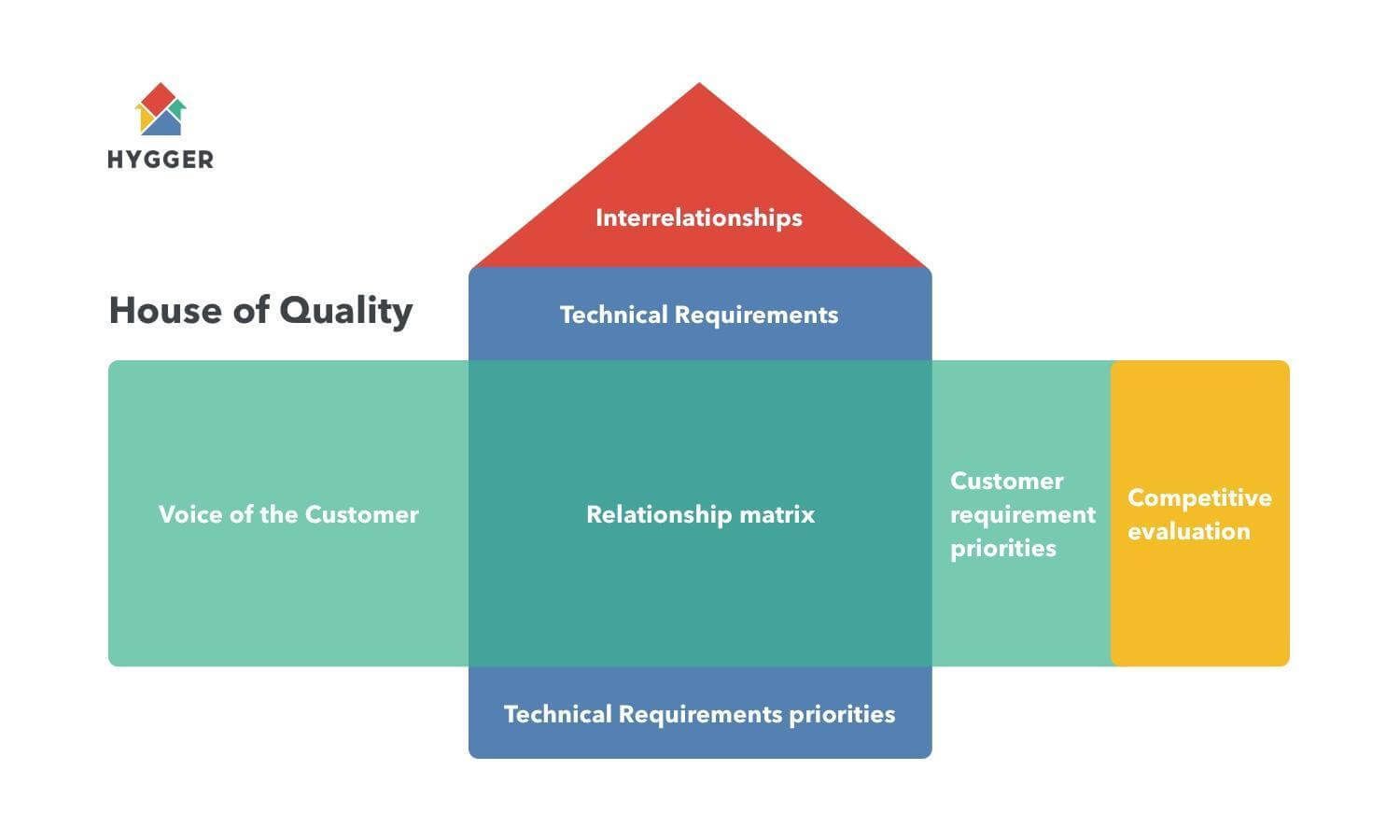
QFD is an acronym that combines functionality from different disciplines, such as management, marketing, and engineering. Quality Function Deployment is typically used for new product design.
It can also focus teams on improving existing products and processes. What are the key advantages of the QFD matrix and what are the components of its visualization, the House of Quality? This brief post covers these fundamental issues.
What is Quality Function Deployment?
Quality Function Deployment is a Lean methodology that is used to identify critical customer attributes and create a particular connection between customer attributes and design parameters.
The matrices used in the concept help design engineers and marketing guys to answer three essential questions:
- What customer attributes are critical?
- What design parameters should be considered while running these attributes?
- What should these parameters target for the new design?
You have definitely heard the term “House of Quality” that represents the QFD framework. It is focused on customer desires and ensures their consideration during the design process and different quality assurance milestones throughout the product life cycle.
The House of Quality
The house of quality is part of the QFD system. As the basic design instrument of quality function deployment, it defines and classifies customers’ desires, identifies their importance, specifies engineering characteristics, and assigns priorities for the system requirements.
The concept is progressed through hierarchical levels of what’s and how’s, analyzing every phase of product growth.
The presumptive result of the House of Quality’s appliance is a matrix with customer desires and correlated nonfunctional requirements.
What every part of the house consists of?
- The left side of the house contains What or Wants. Here customer requirements and needs, as well as priorities, are placed.
- The right side of the house is formed by Competitive Assessment. Here customer priorities are compared with appropriate marketplace offerings.
- The attic of the house is formed by How – technical design features, and characteristics of the offering to meet the customer requirements.
- The roof of the house is represented by Design Relationships that describes the interrelationship between the design features.
- The foundation involves the target values as objective measurements for assessing each characteristic.
What is the History of Quality Function Deployment?
The tool has a 50-year history as the methodology for putting customer needs.
The House of Quality was first used to design an oil tanker in 1972. Yoji Akao and Shigeru Mizuno used the QFD concept to design and manage customer satisfaction. Before the introduction of this innovative tool, the methods of quality control were aimed to fix a problem during or after production processes.
In the 1980s, Don Clausing introduced the concept to the United States (in the automotive industry). That is a famous story about one engineer who tried to place the sports car’s emergency hand brake between a seat and a car door.
However, female drivers disagreed. They wore skirts and had obvious troubles with the new placement of the hand brake. The QFD diagram placed potential dissatisfaction with this functionality location. Therefore, the idea was canceled.
QFD matrix advantages
QFD is useful for companies because it ensures that they bring products to market that customers actually want. It happens thanks to listening to customer preferences at the beginning of the design process and meeting these desires and needs.
Permanent circling back to the client may seem overkilling, however, it quickly identifies any activity that doesn’t work toward the goal of providing products that clients want to purchase.
The overall process looks faster, efficient and less expensive as by limiting product development activities to just the things clients ask for.
This can also increase teamwork and help to avoid competing with internal priorities, as collecting customer inputs and applying them during the product development process is a cross-functional activity.
Are there any disadvantages?
The disadvantages of QFD are primarily connected with seismic changes for some companies with an established process focused on profitability and cost reduction.
Actually, QFD should result in both of those goals but switching the primary motivation to customer satisfaction can meet resistance, especially if the company thinks it is doing a serious job with it.
The customer-focus of QFD can also have some negative repercussions. For example, when clients need to increase production costs or delay technological innovations that can bring advantages in the future.
What is the Quality Function Deployment process?
Considering the process briefly, we can highlight the following details:
- Product planning QFD. With its help, product teams are able to identify offering characteristics, which best meet customer requirements and assist to analyze the rivals’ abilities.
- Component deployment QFD. It is helpful for determining the critical parts and assembly components with the help of prioritized characteristics in QFD1 and it also establishes critical target values.
- Process planning QFD defines critical process operational requirements and elements with the prioritized components in QFD2. It establishes critical process parameters.
- Quality control QFD helps to prioritize the process control methods and parameters and establishes production methods that best support the prioritized process elements of QFD3.
When do we use QFD?
You may apply QFD into the product development process when you find well-understood clients with quantifiably captured desires.
As the main goal of QFD is to ensure a constant focus on the voice of the customer, so it is most effective when it is used throughout the entire product lifecycle.
Quality Function Deployment suits companies that are focused on relatively iterative innovation but not something completely new, because there is a large base of customer feedback to drive the process.
Conclusion
To sum it up, QFD will assist you to achieve the following goals:
- To define the essentials you should put in your product.
- To identify the superfluous aspects that can be removed.
- To prioritize the desires and requirements of your clients.
- To get a vision about your situation in the market.
- To clarify the most important technical features in the product.
- To find out the objectives for the tech features that should be implemented in the future.
Have you ever used QFD in product development? Could you share your impressions? Feel free to comment below.