Defining the Difference Between Lean and Six Sigma
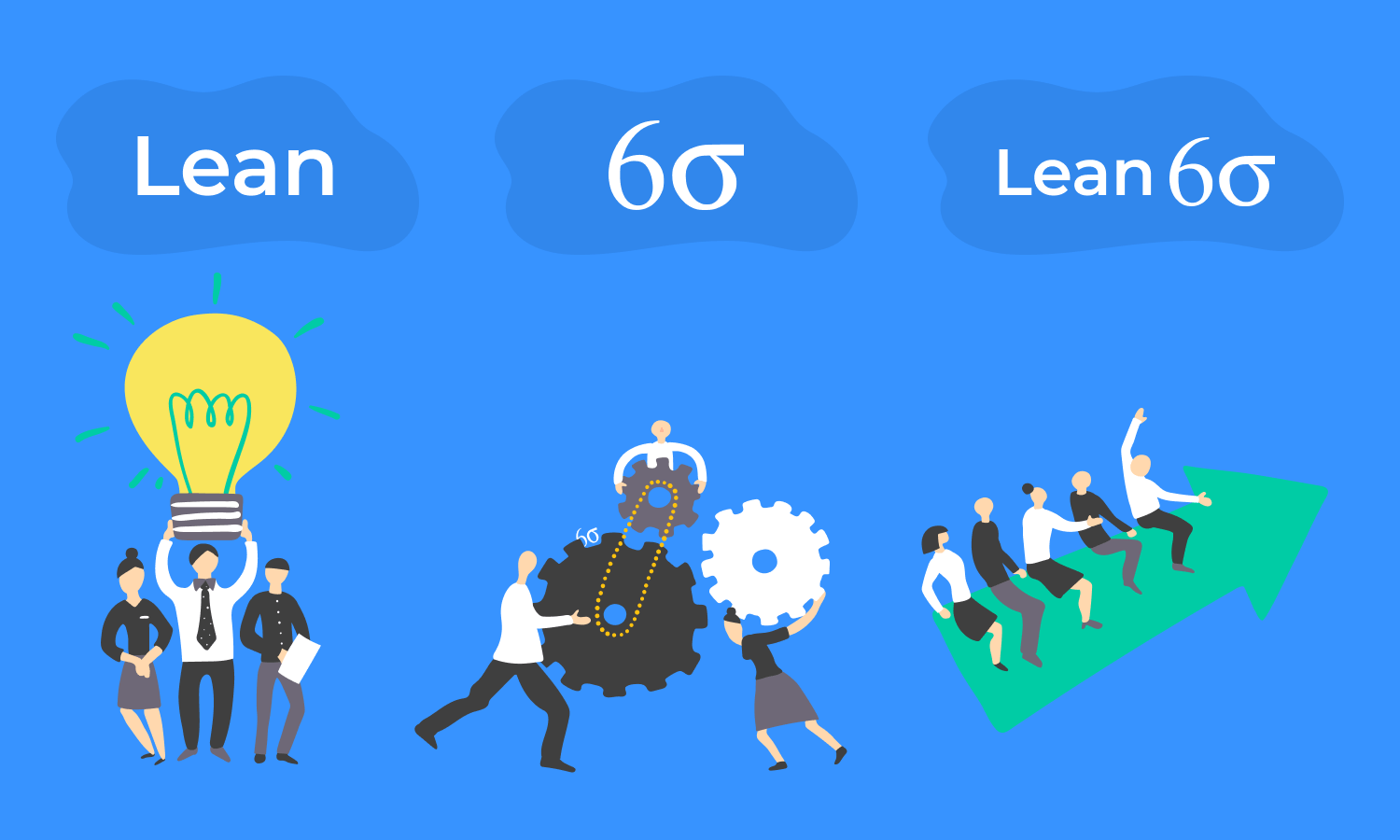
Many companies nowadays still have debates regarding the difference between Lean and Six Sigma, and whether they are mutually exclusive.
Lean is about eliminating wastes, taking time out of processes, and creating better flow. The strategy of Six Sigma is built around the concept that organizations may reach a competitive edge by reducing defects in their commercial and industrial processes.
The two terms have started to blur in meaning, and the reason for that is simple – they both are relatively similar. This post is about the differences and similarities of two approaches Six Sigma vs Lean.
Six Sigma vs Lean vs Lean Six Sigma: let’s start with definitions
- Six Sigma is the original process improvement methodology that focuses on reducing variance and errors in the production process. That is because processes without consistent dependability eventually lead to errors.
- Lean also focuses on process improvement. However, it aims to attack waste. Activities that do not add value to end-users need to be eliminated.
- Lean Six Sigma is a hybrid method that combines the best of both Lean and Six Sigma. Businesses began turning to this idea when they realized they had challenges in areas the separate approaches handle.
The Roots of Lean Manufacturing
Lean manufacturing was initially introduced by Henry Ford. He strived to keep the production standards incredibly high to make every step flowed naturally into the next, resulting in very little waste. Then Toyota company accommodated this process and developed its own production system that became one of the most effective in the world.
The key difference between Lean and Six Sigma approaches is that they view the causes of waste in completely different ways.
The goal of Lean is to reduce waste by eliminating bottlenecks and improving the quality of products. The method identifies 7 areas of waste that seem common for many production systems. Here they are:
- Overproduction happens when products are being produced that there is no customer demand for.
- Waiting means the lag time in between every step in production.
- Transport. When products/materials are moved inefficiently, this waste occurs.
- Motion is when employees moving inefficiently between tasks. It means poor work standards.
- Over-processing happens if people spend too much time producing a product.
- Inventory is when you have too much work in progress at one time.
- Defects are connected with the time employees spend identifying and fixing production mistakes.
When you implement the Lean approach, your team members will be able to move materials less frequently. It will definitely improve the quality and require less overall inventory. You’ll be able to deal with quality issues during the manufacturing process and save time and resources.
These improvements will result in a more successful manufacturing process. Your clients will have a more satisfying experience because the products will be produced and delivered on time.
The Roots of Six Sigma
The history of Six Sigma comes to the 1980s. Bill Smith who worked for Motorola introduced it.
Unlike the Lean approach that is predominantly used in production, Six Sigma can be applied to reduce errors in both production and nonproduction environments.
Six Sigma tools are aimed to decrease the level of waste. It determines defects as anything that doesn’t meet the customer’s expectations.
The framework is focused more on eliminating variations in customer experience. A company that performs in accordance with Six Sigma will produce no more than 3.4 defects for every million opportunities. Bill Smith, the author of Six Sigma believed that by getting rid of variation people can improve the customer experience and increase their savings.
After Motorola’s success, many companies all over the world have adopted Six Sigma.
Another key difference between Lean vs Six Sigma is that each method implements process improvement. Six Sigma does it by using DMAIC.
DMAIC means define, measure, analysis, improvement, and control.
- Define is the first step where you’ll have to identify the problem and learn how it is affecting the current process.
- Measure is the next step, where you measure the current data. By exploring the current process and determining what isn’t working you will be able to find a way to make improvements.
- Analysis will help you to get to the root of your problem.
- Improvement is the step where you work with possible solutions, test them, and make improvements as needed.
- Control stands for continuing to make improvements over time.
Six Sigma vs Lean: What is the difference?
We have mentioned some evident differences between Six Sigma vs Lean above, however, they both work toward the same ultimate goal: to eliminate waste and create efficient processes.
The truth is that two approaches take different ways on how to accomplish this:
- Six Sigma focuses on almost perfect results that will decrease costs and achieve higher levels of customer satisfaction.
- Lean is aimed to analyze workflow to reduce cycle time and eliminate waste. It strives to boost value to customers while using a few resources as possible.
Wrapping up
To summarize this, the core difference between Lean vs Six Sigma is that the Lean framework looks at ways to increase flow while Six Sigma aims to achieve consistent results.
Actually, they both demonstrate that it is possible to significantly improve the quality of a particular product and customer experience by improving processes.
Logically, when companies try to improve inefficient processes they strive to choose only one method going forward. After all, the main idea is how you can take the elements you like from each approach and apply them to solve your business’s problems.