5 Essential Lean Metrics To Improve Work Flow
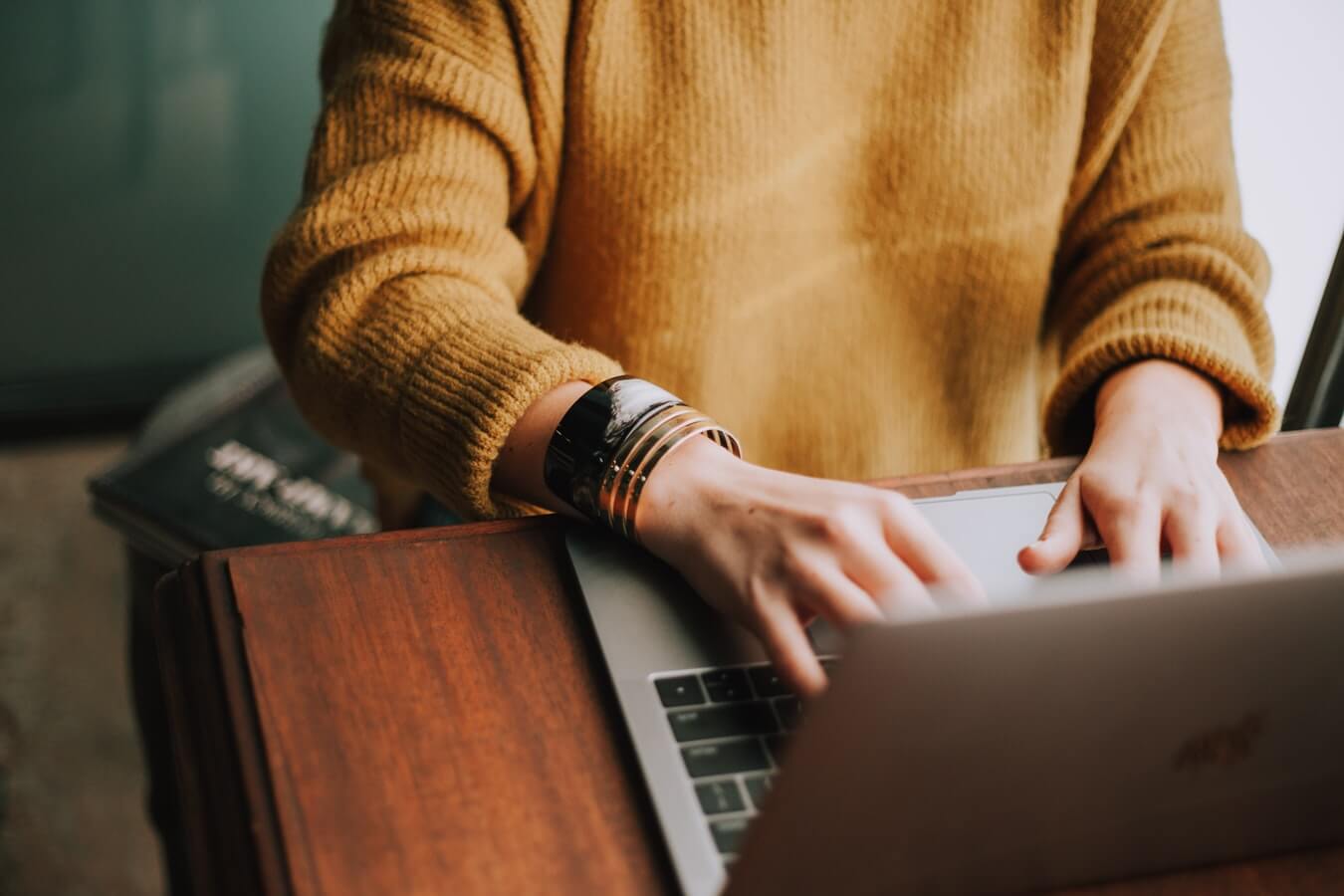
Contrary to a popular belief, though Lean was originated from the Japanese manufacturing industry, today it can be applied to every business and every process. Being Lean means ensuring everything you do in your work processes adds value. This philosophy has turned Lean into a widely-used approach to identify wasteful practices, reduce costs, and increase quality.
Henry Ford defined the Lean concept in one sentence: “We will not put into our establishment anything that is useless.” Going into more detail, the term “lean manufacturing” is used to describe a systematic method for the elimination of “waste” (defects, overproduction, etc.) within a manufacturing system to improve customer value – because “value” is the only thing customers are willing to pay for.
Lean is based on five key principles: value, value stream, flow, pull and perfection.
- Value is defined by the customer’s needs for a specific product (e.g. timeline for manufacturing and delivery, price point, etc.)
- Value stream is all the steps and processes involved in taking “raw materials” and delivering the final product to the customer. This includes drawing a ‘process map’ to identify steps that don’t create value and eliminate them.
- Flow means making sure all steps that remained after the value stream occur with no interruptions, delays, or bottlenecks. In other words, the product or service must flow smoothly toward the customer.
- Pull means delivering products “just in time” – the customer can “pull” the product from you as needed.
- Perfection is about making Lean thinking and process improvement part of your corporate culture.
From now on, we’re going to focus on flow that refers to the manner in which work progresses through a system.
A good consistent flow where work is done steadily and predictably (vs bad flow where work stops and starts frequently) is essential for a fast and reliable delivery and bringing greater value to your customers, team, and organization. This is the reason why many teams use Kanban boards to visualize work in progress and identify flow problems.
Combined with Kanban boards, Lean metrics provide a valuable insight, helping improve your processes and deliver more quickly. The most essential metrics include:
#1. Work in Progress (WIP) and Work in Process
Work in progress is the total amount of work you have committed to but have not completed at any one time. Work in process is all the work that is actively being worked on at any one time.
If you’re new to measuring flow, start with work in process. Count and record the number of unfinished cards (work items) in your system each week to understand how much work is in process and therefore not yet providing value. WIP can be measured in one of two ways, either by counting the cards on your board or by using a cumulative flow diagram.
#2. Queues
Queues are formed when work waits between different stages. Limiting the time that work spends in queues can help reduce your overall cycle time and keep work flowing through the system.
Use efficiency diagrams to identify where work gets stuck. Investigate what can be done to minimize the amount of work you have in queues, relative to the total WIP in the system.
#3. Blockers
Blockers indicate work that cannot move forward in the process. Compared to work in a queue – which is simply waiting its turn to be pulled into process — a blocker is typically a failure condition that requires immediate attention.
Count how many items are blocked and how long they stay blocked. Work to reduce both numbers to improve your flow.
#4. Lead Time and Cycle Time
Lead time measures the total time it takes for work to move through the value stream – from the moment the work is requested to the time it’s delivered. Cycle time measures how long it takes a work item to get from point A to point B.
These are useful metrics for understanding how long it takes for work to flow through your system. By tracking and comparing these metrics over time, you can view trends, evaluate changes and improve your delivery capabilities.
#5. Throughput
Throughput is the average number of units processed per time unit. In a Kanban system, examples can include “cards per day,” “cards per week,” or “story points per iteration.”
It’s important to track and measure throughput as it impacts your business decisions. Combined with other metrics, throughput is a reliable way to make short-term predictions and even forecast delivery dates.